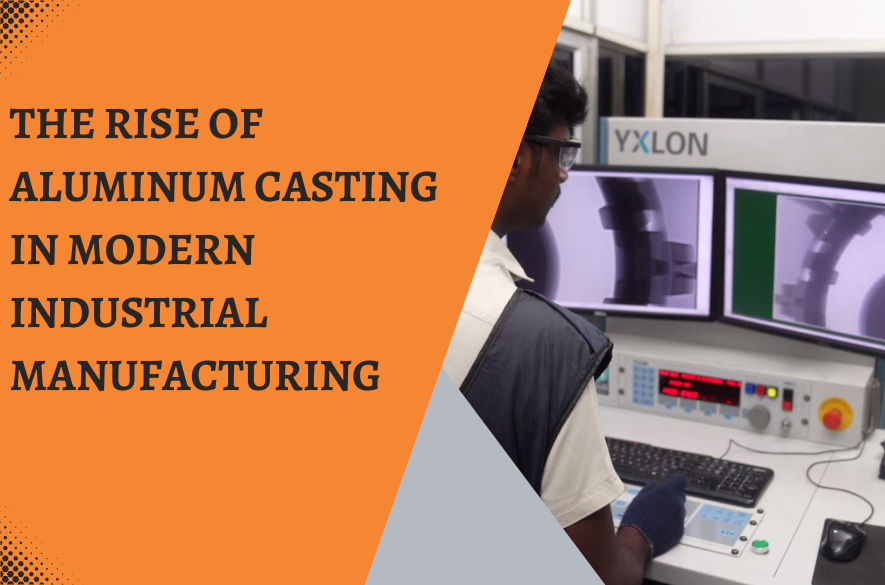
The Rise of Aluminum Casting in Modern Industrial Manufacturing
Aluminum casting has evolved far beyond simple, cost-effective mass production. Today, it's about delivering precision, strength, and unparalleled customization. Modern aluminum casting companies are dedicated to providing high-performance components that consistently meet the most stringent industrial standards. Whether the requirement is for intricate, complex designs or large-scale mass production, these companies, including Roots Cast, are equipped to deliver with exceptional accuracy and consistency.
1. Proven Industry Expertise
One of the key drivers behind the significant growth in aluminum casting is its remarkable versatility. From durable housings for LED lights to critical automotive components like brackets and manifolds, aluminum castings have become an indispensable requirement across a multitude of applications in various industries.
Innovation Through Advanced Die Casting Technology
Leading aluminum die casting manufacturers in India are at the forefront of innovation, embracing advanced technologies such as:
- Tilt Pour Casting: Ensures consistent metal flow for superior quality components.
- Permanent Mold Casting: Delivers increased strength and excellent repeatability for high-volume production.
- High-Pressure Die Casting: Achieves incredibly close tolerances and a remarkably smooth surface finish, minimizing post-processing.
At Roots Cast, these sophisticated procedures ensure that our components are of world-class quality, significantly reducing the need for post-manufacturing processing. This strong emphasis on continuous innovation has firmly established Indian manufacturers as the preferred choice for Original Equipment Manufacturers (OEMs) around the globe.
Sustainability and Efficiency: A Core Commitment
Another significant strength of the aluminum casting industry is its inherent sustainability. Aluminum is 100% recyclable, and modern casting methods are designed to minimize material waste and optimize energy consumption. The majority of Indian aluminum die casting manufacturers, including Roots Cast, are committed to employing eco-friendly practices such as:
- Closed-loop recycling systems: Maximizing material reuse and minimizing environmental impact.
- Energy-efficient furnaces: Reducing energy consumption during the melting process.
- Reduced emissions: Implementing processes that lower harmful emissions during casting.
These green practices not only benefit the environment but also contribute to significant cost-effectiveness and enhance the brand value for our clients, aligning with global sustainability goals.
Meeting and Exceeding Global Quality Standards
To compete effectively on a global scale, aluminum die casting manufacturers in India are making substantial investments in:
- In-house tooling facilities: Ensuring precise and high-quality molds for accurate parts.
- Automated quality control systems: Implementing advanced systems to detect defects and maintain consistency.
- Internationally recognized certifications: Such as ISO 9001 and IATF 16949, demonstrating a commitment to world-class quality management.
This comprehensive approach results in the production of defect-free components that consistently meet tight tolerances and complex dimensional requirements, which is especially critical for industries where safety and reliability are paramount.
Conclusion: Shaping the Future of Industrial Production
The passion and creativity of aluminum casting companies are undeniably shaping the future of industrial production. With their unwavering emphasis on perfection, sustainability, and technical excellence, aluminum die casting manufacturers in India are not only meeting global standards but are actively setting new benchmarks for the industry. Companies like Roots Cast are becoming the first-choice partners for high-quality cast components, heralding a new era of reliability and performance in the world of metal casting.