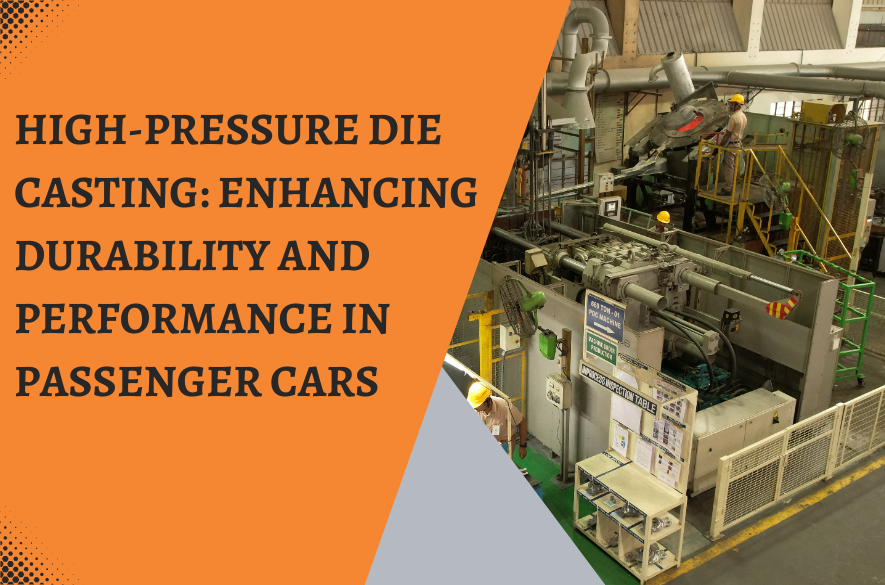
High-Pressure Die Casting: Enhancing Durability and Performance in Passenger Cars
The automotive sector has undergone tremendous change in recent years, with durability and performance becoming defining characteristics that celebrate high quality passenger cars. High- pressure die casting has emerged as the leading technology for producing durable, process- efficient, and widely used automotive components with good surface finish and high dimensional accuracy. Contributing to better structural integrity and efficiency in fuel consumption in passenger cars, the High Pressure Die-Casting parts have emerged as essential for modern vehicle manufacturers, who are in a quest to push innovation to its limits.
What is High-Pressure Die Casting?
High pressure die casting is a versatile manufacturing process where molten aluminum metal is injected into a mould cavity under high pressure. This process can produce large quantities of parts in a short time frame, often making it the most cost-effective option for high-volume production runs. The speed and precision of casting cycles ensure reduced waste, increased efficiency, and, ultimately, lower cost per unit over time. Automotive die-casting manufacturers can, therefore, meet the ever-increasing demand for reliable and high-performance automotive parts with a superior surface finish and high dimensional accuracy. The ability of high-pressure die casting to produce complex shapes with minimum machining further justifies this process for the manufacturing of die-casting parts for passenger cars.
Advantages of High-Pressure Die Casting for in Passenger Cars
Superior Strength: The high-pressure process ensures that die casting parts for passenger cars are exceptionally tough and capable of withstanding significant wear and tear. Some of these parts are crucial to enhance the life expectancy of the vehicle. For instance, components such as engine housings and transmission systems benefit greatly from this manufacturing method, as they require high strength and resilience to endure the harsh operating conditions they face.
Lightweight design: The automotive die casting manufacturers have been focused on producing lighter components to improve fuel efficiency. A part produced with high-pressure die casting is designed to be a lightweight but also sturdy piece, which helps automobile manufacturers considerably reduce the overall weight of automobiles without compromising strength or durability. Thus, the weightless parts produced through high-pressure die casting are essential in the pursuit of more sustainable and efficient automotive designs.
Accuracy and Performance: The manufacturing process includes several components crafted with precise accuracy, a critical attribute in modern passenger cars. High accuracy ensures that engines run smoothly and efficiently, reducing friction and wear. Automotive die-casting companies depend on advanced technology to produce these vital parts, which enhance vehicle performance without sacrificing durability. By using high-pressure die casting, manufacturers can create intricate components that meet exact specifications, ensuring a balance of reliability and high-quality performance in today’s automobiles.
Role of Die Casting Components in the Future of Passenger Cars
Automotive technology developments are increasingly reliant on high-quality, precision- engineered components. In this context, passenger car die-casting parts have played a vital role.
From engine components to transmission systems, these parts are integral to the functionality of next-generation vehicles. With growing concerns over sustainability, automotive die-casting manufacturers are also adapting to the green manufacturing trend by utilizing recyclable materials, thus reducing their environmental impact.
In conclusion, high-pressure die casting represents an innovation that not only provides strength to vehicles but also ensures their operational efficiency. The advanced technologies implemented in the die-casting process are paving the way for a more sustainable and efficient automotive future, enhancing both performance and environmental responsibility in the industry.